Modernizing the information system for technical documentation and after-sales processes
What was the challenge?
PSA, now grouped under the Stellantis banner with the Fiat Chrysler Automotive group, produces a large quantity of documentation for people involved in the maintenance and repair of its models. The after-sales department, which used a cumbersome and costly system, resulting from many years of reorganizations, industrial mergers and the addition of successive business layers, wanted to modernize its processes. The goal was to optimize its production and to comply with the group’s directives on digital transformation. The project consisted of the complete overhaul of the production and distribution chain of technical documentation, including repair manuals, parts catalogs, bulletins and intervention time frames.
Definition:
DTD stands for Documentation Type Definition. It is a set of rules defined to structure a document, notably with the help of tags, or more simply with the names of sections, paragraphs, etc. In this way, several documents that use the same DTD will have a perfectly identical structure.
Until then, the production of all these deliverables was carried out using a Word-based solution, nevertheless constrained by a <a href=”#definitiondtd” target=”_blank” rel=”noopener”>DTD</a> that guaranteed a first level of uniformity.
The PSA teams also had a huge repository of texts, phrases and expressions that they called a thesaurus. This terminology base lessened the need to create content, generated a translation memory that reduced costs and accelerated the localization of manuals available in 30 languages.
At the same time, images and illustrations were stored in a simple file system, which did not facilitate collaborative versioning and referencing of images in documents.
Maintaining an efficient and demanding <strong>technical documentation</strong> solution using primarily a word processor such as Word created many pitfalls during intensive production. Firstly, although it is one of the most recognized word processors on the market, Word is not designed to generate documentation of several hundred pages, and therefore had shortcomings when processing large volumes. Secondly, it is a heavy client, with all the problems of managing its maintenance and tracking licenses. Thirdly, the interface between Word and the thesaurus had its limits, although the end result was entirely satisfactory, it was also time-consuming for the technical writing teams, and involved many cycles of proofreading and verification to ensure proper usage. Basically, it gave with one hand what it almost took away with the other, but its overall value made it a critical tool.
Lastly, and this was the main constraint of the project, it was essential to modernize the production line, without ever causing a loss of service for the users.
What solution could be found to help the company and its technical writers ?
In 2016, 4D Concept was asked to respond to these issues and provide PSA with all its expertise in document engineering and digital transformation.
The impossibility of overhauling the entire system in one go was an essential constraint in order to avoid any risk of interruption. The 4D Concept teams therefore built a smooth migration plan to replace each module, business and solution, progressively. The approach using Agile methods allowed us to continuously validate each change and development by keeping what was positive in the existing tools, information or data while maintaining the quality requirement for the technical documentation.
It was primarily the authoring tool that was the focus of interest. The use of a reliable, robust, modern, connected, collaborative and above all well-designed solution for the structured authoring of high technical value content became essential, and even urgent. To that end, 4D CONCEPT was delighted to propose the use of its ADAM Author software, which had successfully proven itself in equally sensitive sectors such as aeronautics and defense. Coupled with the <a href=”https://adam.4dconcept.fr/manager/”>ADAM Manager</a> CMS, ADAM Author’s great data exchange capacities allowed it to be quickly connected to the various existing PSA databases. Quick connection guaranteed continuity of use and content supply, and facilitated the writing process thanks to the autocompletion feature. In addition, ADAM Manager can progressively recover illustrations as they are used, so it was able to gradually free itself from the file system.
Furthermore, ADAM Author and ADAM Manager together offer a range of features to facilitate the integration, management and versioning of illustrations and other technical documentation elements. Each image file could now be referenced and the update of an image would automatically impact all content referencing the illustration concerned. The two software solutions also offer usability features such as drag and drop to make the work of technical writers easier. What’s more, ADAM Author guides them to ensure compliance with the DTD in place, and then performs audits.
The second step implemented opend the way to replacing another business module: the publication of bulletins. The so-called Service Bulletin is particularly sensitive in terms of protection. It alerts all the repair and maintenance actors to changes in procedures, tools or parts reference, consumables, or to any malfunction that may lead to implementing a recall campaign. The authoring and publication of newsletters must therefore meet very high standards of quality, requirement and reliability by following a particularly complex work stream. To implement it, 4D Concept has deployed Heysquid. As it is equipped with a powerful workflow engine and extensive print and web publishing capabilities, Heysquid not only controlled the newsletter production process, but also progressively retrieved and indexed the illustrations needed to produce the bulletins.
The next steps replaced other functional areas:
- the interface for maintenance and repair professionals to view technical documentation.
- the mechanisms for managing the publication of service time frames, catalogs and repair manuals either in this order or according to the priorities set with the PSA-Stellantis teams.
What were the benefits for users?
While the development and deployment of these solutions offered many improvements to users by making authoring tasks easier, the most obvious benefits were to the process as a whole. It was spectacularly simplified and, above all, made secure. The process fluidity and the savings generated will have a snowball effect on the group’s overall performance as the effect of these gains filter through to margins and prices.
In addition, the smooth migration process, per functional area, made it possible to secure production and avoid any disruption.
The company
PSA is a group that has its origins in the merger of several century-old French car brands, Peugeot and Citröen. Over the years, the group has brought together different industries and historical processes with different technologies, and for many years has been faced with the need to standardize its tools and work methods. The efforts made are aimed at pooling all synergies and, above all, preparing for the future by making savings at all levels to improve the group’s profitability.
In the broadest possible sense, this is the challenge facing the entire automotive sector today. Most of the major brands are grouped together in huge, international groups, which have to find the best solutions to guarantee the common operation of thousands of employees, hundreds of factories, and numerous brands often with different DNA, and thus rationalize the stacking of heterogeneous technical procedures.
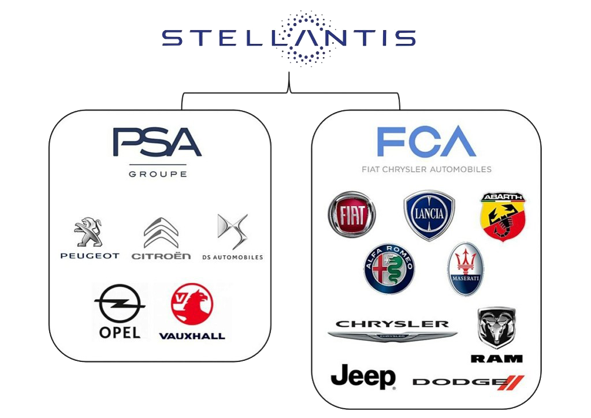
It is to that end that PSA initiated and developed several major business plans impacting all levels of the group, including the strategic plans “Back in the race” and “Push to pass” which were aimed respectively at operational excellence and profitable growth initiated by Carlos Tavares.
And it is in the context of the second plan that the group’s desire to overhaul a certain number of its production tools fits in, in order to guarantee the efficiency of its systems in a context of growth, while benefiting from all the opportunities that change and technological evolution can bring.
Digital transformation, as much for the dematerialization of certain activities, as for making contact and keeping in touch with the customers, was promulgated as the first base of the “Push to Pass” plan.
Why 4D Concept?
The work collaboration between the PSA Group and 4D Concept on issues related to technical documentation is not recent. Just before the year 2000, several projects were initiated, gradually making 4D Concept a partner of growing importance until it became the sole provider for the production of all content and on-board technical documentation for the group’s vehicles.
The after-sales teams were interested in 4D Concept’s solutions, particularly the use of 3D data from digital modelling to assist in the writing of technical content. The integration between ADAM Author and Catia Composer represented a real opportunity to include documentation in the <strong>Industry 4.0</strong> project led by PSA. And it was in this context that the global migration project was developed and launched to set up a form of digital continuity for developing and implementing the fundamental shift towards the industry of the future.